Specialized high-strength synthetic macro fibers for precast concrete are our company's key products.

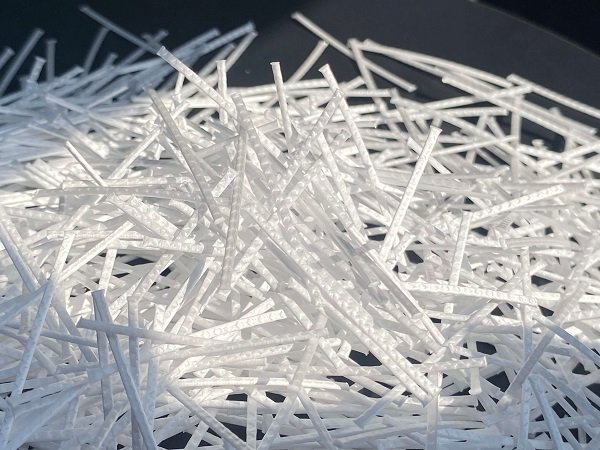
Specialized high-strength synthetic macro fibers for precast concrete are manufactured using our company’s unique drawing process. The product’s tensile strength exceeds 650 MPa, and its elastic modulus exceeds 10 GPa. These fibers are primarily used in tunnel segments, high-strength concrete piles, square piles, ballastless track slabs, embedded track slabs, floating slabs, stadium precast seats, precast concrete boxes, and almost all precast concrete components. Domestically, we are the first company to produce high-strength synthetic macro fibers with a tensile strength exceeding 650 MPa. We collaborate with major companies such as China State Construction, China Railway Construction Corporation, Shanghai Tunnel Engineering Co., Ltd., and China Communications Construction Company in the high-strength precast concrete component sector, participating in over 200 projects and accumulating tens of thousands of hours of production experience. We have established a standardized production model to ensure consistent quality for every batch of products, rather than relying on individual technicians’ production experience. Serving global customers is our next goal.
We can provide unique synthetic macro fiber designs for tunnel segments, large precast concrete components, and all precast concrete elements for rail transit, including both above-ground and underground structures.
Specifications and Services for Special High-Strength Synthetic Macro Fibers for Precast Concrete:
Tunnel and rail transit projects require different engineering solutions based on geographical conditions and construction requirements. We use international concrete standards as a basis and then design exclusive high-strength synthetic macro fibers for different precast concrete components based on specific construction needs. These designs are not based on specific standards but are determined by the performance requirements of the precast concrete components. We will assist the construction party in tailoring specialized high-strength synthetic macro fibers, assist in designing mix ratios, and provide tracking services until the concrete components are demolded.
The advantages of using our high-strength synthetic macro fibers for precast concrete components and track slabs.
High-strength synthetic macro fibers enhance crack resistance and the integrated reinforcement is not affected by tensile stress.
High-strength synthetic macro fibers for concrete have high tensile strength and elastic modulus, which can improve the impact resistance of precast concrete components. With 40,000 fibers per cubic meter of concrete arranged in a three-dimensional structure, these fibers provide overall reinforcement, ensuring worry-free post-installation activities (such as drilling for tunnel segments or post-treatment of track slabs). Additionally, they reduce minor spalling during transportation.
By creating rhomboid physical indentations on the fiber surface, the contact area between the fiber and concrete is increased, enhancing their bond. This prevents deformation or cracking under any directional tensile stress. Fiber-reinforced concrete allows for the production of concrete components in different shapes (such as curved tunnel segments or spring-loaded floating slabs). High-strength synthetic macro fibers can easily withstand tension from any direction.
Adding high-strength concrete fibers simplifies the initial maintenance of precast concrete components. The fibers’ crack resistance reduces the occurrence of microcracks.
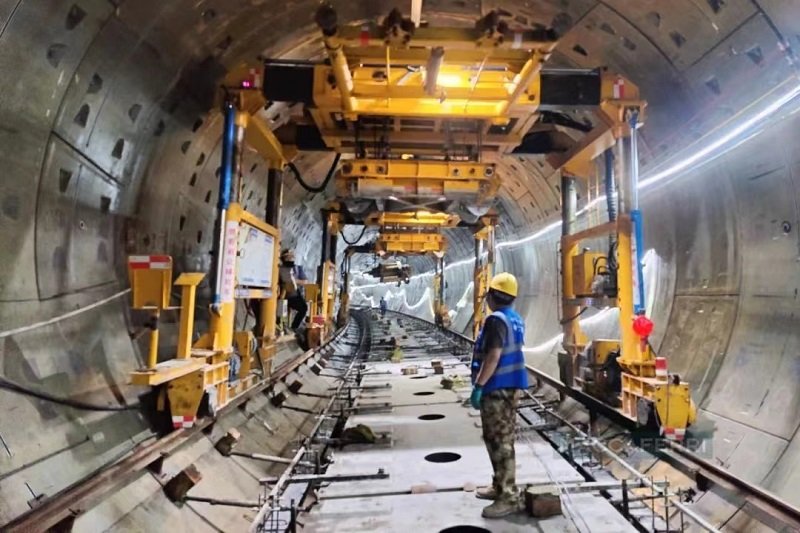
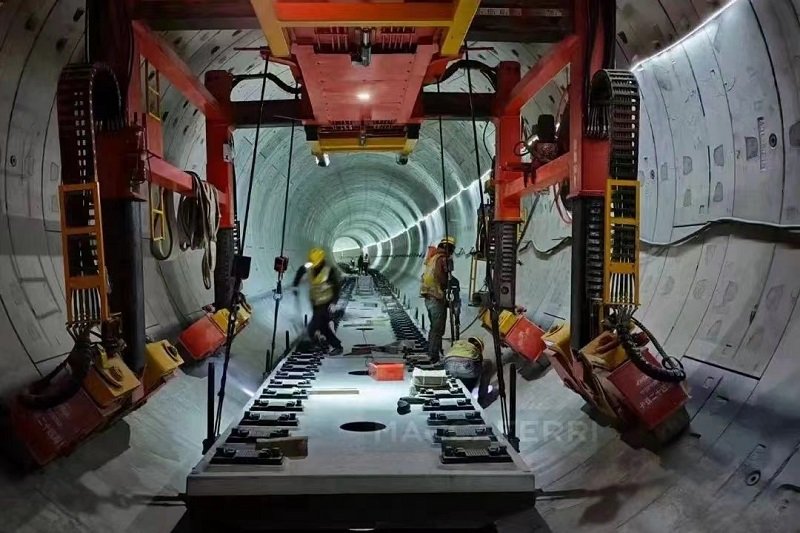
Improves precast production speed, reduces costs, decreases maintenance expenses, and increases the lifespan of precast concrete components.
The use of high-strength concrete macro fibers aids in the early hardening of precast concrete components, thereby shortening the demolding cycle and increasing production efficiency. High-strength synthetic macro fibers can also reduce the weight of concrete components, lowering transportation costs and overall project expenses. Using these fibers instead of steel reinforcement reduces the conduction of track currents, corrosion of tracks, and increases the lifespan of transportation facilities. Additionally, the use of concrete track slabs increases road construction speed, shortens construction time, reduces costs, and decreases future maintenance expenses.